From design to delivery: fast-tracking charger development on-site at Prodrive Technologies
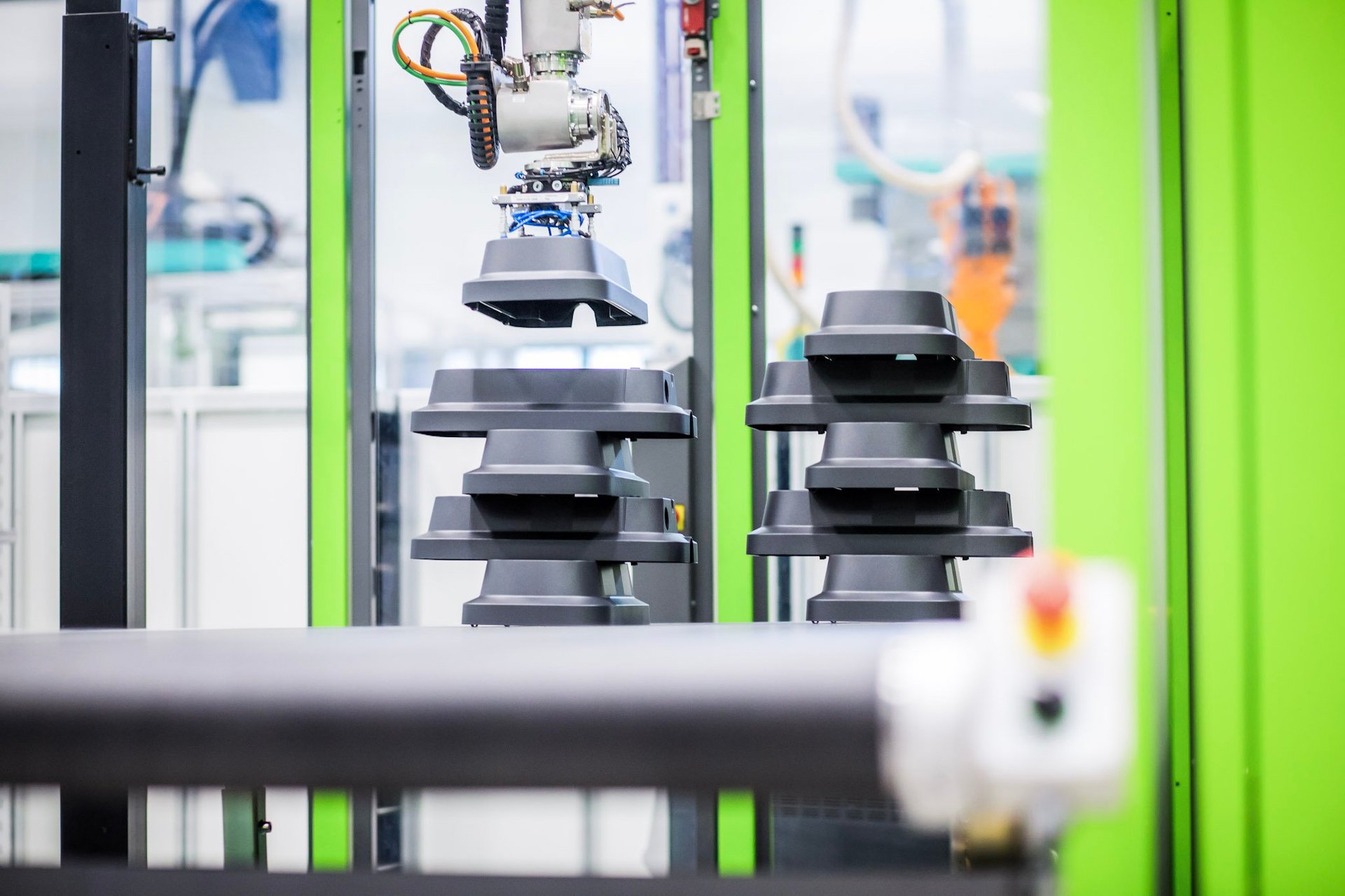
When it comes to developing white label EV chargers, having an on-site testing facility is a great advantage. Backed by our parent company Prodrive Technologies, we have all the resources in-house to quickly adjust designs when needed and collaborate closely with clients at each stage of the process. This approach ensures we deliver high-quality chargers that perfectly meet every client’s specifications.
1. Faster time-to-market
Bringing products to market faster is critical in today’s competitive landscape and on-site testing during the development and validation stage speeds up the process.
Environmental testing methods like highly accelerated lifetime testing (HALT) and thermal shock require in-depth testing in climate changers to simulate years of real-world usage, ensuring the end-product is ready for real world environments.
Our integrated facility also simplifies the certification process, and pre-certification testing allows us to handle most regulatory checks internally during the development stage before reaching out to external certification bodies, accelerating the overall time-to-market.
2. Building strong client partnerships
For our white-label clients, access to our factory, where the chargers are manufactured, isn’t just convenient, it offers unmatched transparency. By visiting our facility, you can see the final stages of the testing process up close as the products near the end of the production line.
Take charge point operator, STROOHM, for example. During a facility visit, the team saw first hand the production process of our chargers, before being rebranded as their ZenCharger, the perfect white label product for their needs.
Seeing the product’s durability and quality firsthand strengthened their confidence and cemented trust in our partnership, with Bart Massin, CEO at STROOHM, stating “when you see the testing in real life, you instantly understand how the 10-year warranty is given.” This level of transparency ensures that our white label process aligns perfectly with each client’s vision.
3. Adapting quickly with real-time testing
When challenges in design or functionality arise, we can tackle them right away. Whether it’s tweaking a design or resolving issues uncovered during environmental testing, we can test solutions on the spot without waiting for third-party input. This quick turnaround is especially valuable when developing new charging solutions, as changes can be made immediately, saving time in the process, and ensuring the chargers are fully tested before they are developed for white label products.
“Having access to testing facilities close by allows us to go from design to a functioning product very quickly. The threshold to start testing is lower when you don’t have to outsource - you just ask the test engineer and within a day, your test is running.”
Bram Schroeders, Mechanical Engineer
4. Raising the bar for cross-team collaboration
From manufacturing the printed circuit board assembly (PCBA) to putting together the final EV charger, our team controls every step of the process. This means every process, including our rigorous testing procedures, is executed to the high standards we set for ourselves. Our engineers can be confident that the products meet performance standards before they reach consumers and even frequently test beyond certification requirements for extra peace of mind.
This hands-on approach also fosters collaboration between teams at Peblar. With design and testing so closely integrated, innovation flows smoothly from concept to finished product.
5. Driving continuous R&D and innovation
With years of experience from Prodrive Technologies, our engineers can leverage valuable research and insights to continuously drive innovation forward. We regularly test new features like solar charging under real-world conditions and adjust designs based on results. This feedback loop between development and testing accelerates product evolution and keeps Peblar chargers future-ready with new features and integrations. It means every new feature is not only functional but also market-ready in a fraction of the time it would take with outsourced testing.
“Every time before we roll out new firmware, we test it for weeks in our own parking lot, and with colleagues at home. Once we have them in the open for the very first time, we can see if everything works as intended before it goes to our customers.”
Niels Klemans, System Test Engineer
Delivering excellence every time
On-site testing at Prodrive Technologies transforms how we develop white label EV chargers, speeding up development process and making us more agile. These years of experience from our parent company have made us fast, thorough and ahead of the curve. To find out more about the quality of our white label chargers, view our information brochure.