Every Peblar charger is designed, manufactured and tested in our fully vertically integrated facility at Prodrive Technologies in Eindhoven, the Netherlands. Take a journey through the sections for a look into our production line and the robust tests we put Peblar chargers through. After all, we believe excellence starts with quality you can trust.
Production
We take pride in building our PCBAs in-house. Our PCBA production line assembles 1200 components per device, making it the heart of every charger. After every step in this process, the PCBA undergoes rigorous testing to ensure the highest quality in each EV charger
STAGE 1
Printed circuit board assembly (PCBA)
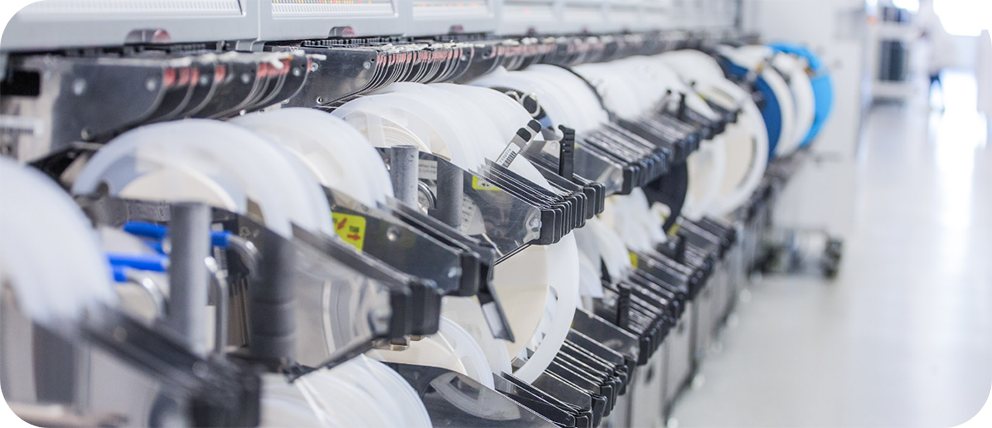
We begin the PCBA process in the surface mounted device (SMD) department, where small components are carefully soldered onto the PCB. This process requires the utmost precision and consistency, so we perform visual inspections and X-ray checks throughout this step
STAGE 2
Through-hole soldering
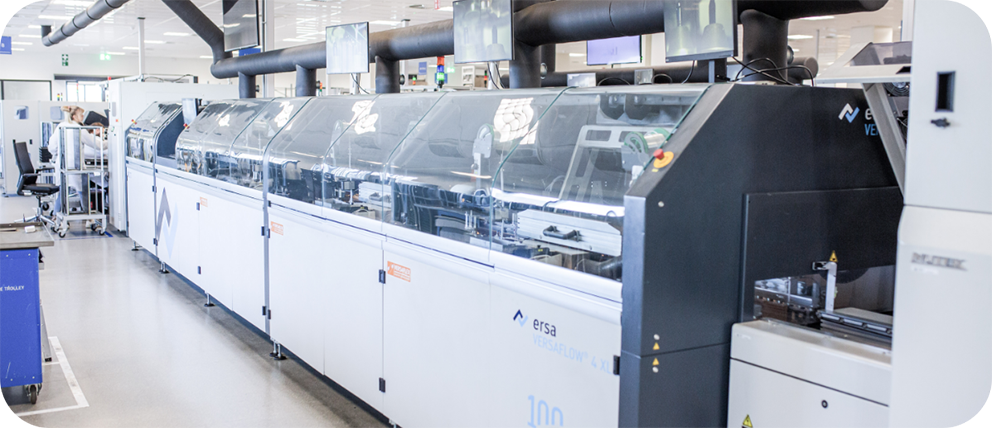
In the through-hole line, we solder larger components such as relays, residual current devices (RCDs) and big connectors onto the PCB. We run automatic electrical tests (AET) using the bed of nails method; the PCBA is positioned between two plates and electrical probes make connections to the board.
This setup flashes the firmware onto the board and ensures that all components are correctly placed. After soldering, we carefully inspect the quality of the solder joints to confirm all components are correctly placed
STAGE 3
Injection moulding
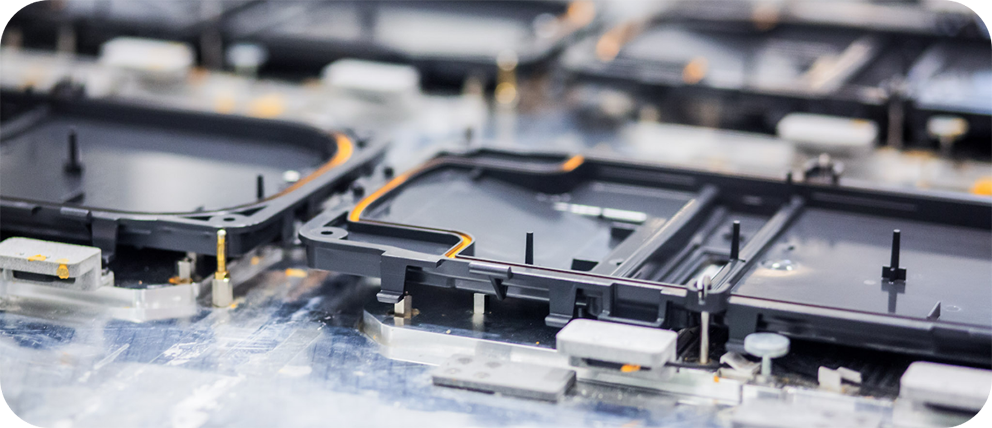
At this stage, all the plastic parts are made using advanced steel moulds. These components have several functions: impact resistance, water and dust protection, display functionality to show charger status and internal features to ensure easy installation and PCBA protection.
This plastic housing embodies the signature elegance and authentic design at Peblar.
STAGE 4
System assembly
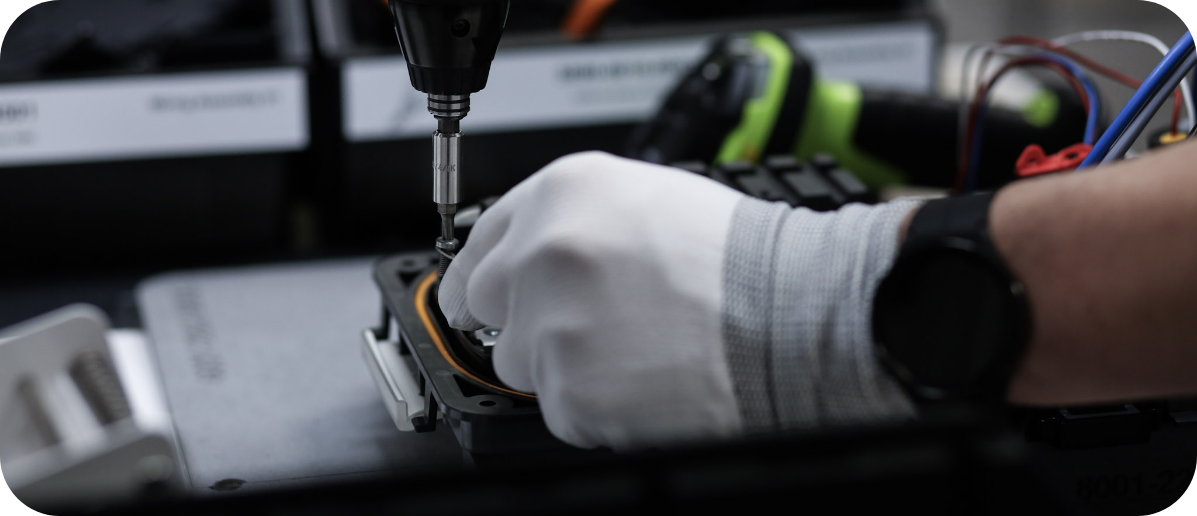
In the next stage of the charger assembly, we fit all the mechanical parts and PCBs into the EV charger. We also perform automated visual inspections (AVI) to ensure the product is correctly assembled according to our quality standards
STAGE 5
Energy meter test
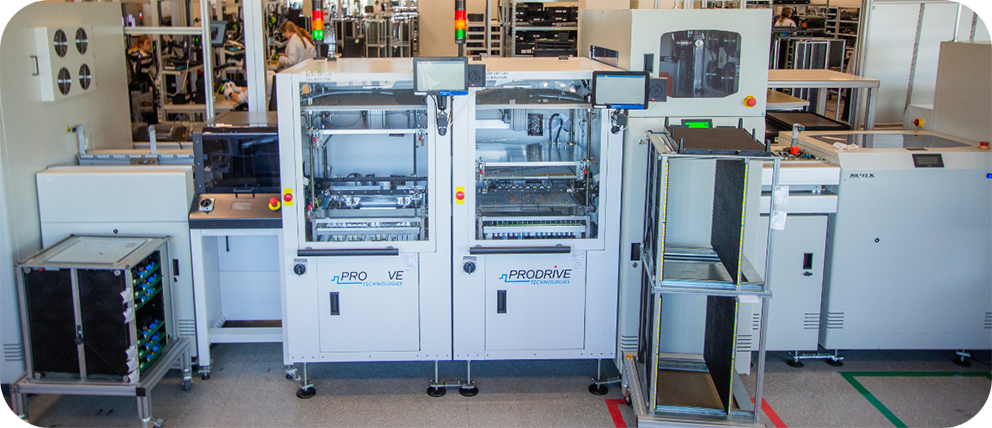
In one of the final testing phases, the integrated energy meter is tested. Once the chargers are plugged in we verify that the integrated energy meter accurately measures the charged energy and complies with the Measurement Instrument Directive (MID) and the German Eichrecht regulation (MessEG).
STAGE 6
End-of-line test
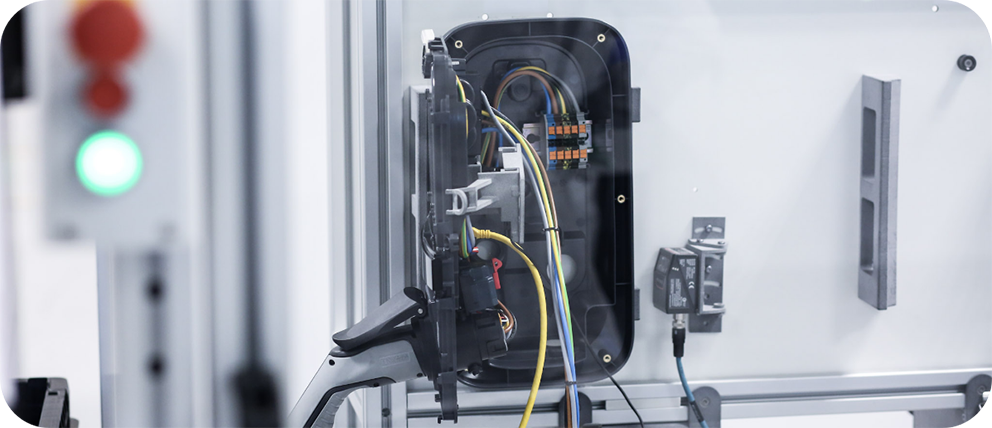
Next, we power up the charger to test the whole system's functionality. We test for current leakage, ensure the radio frequency identification (RFID) communicates flawlessly, and confirm the socket assembly is secure. Even the charger display undergoes examination to make sure everything operates as it should
STAGE 7
Firmware programming
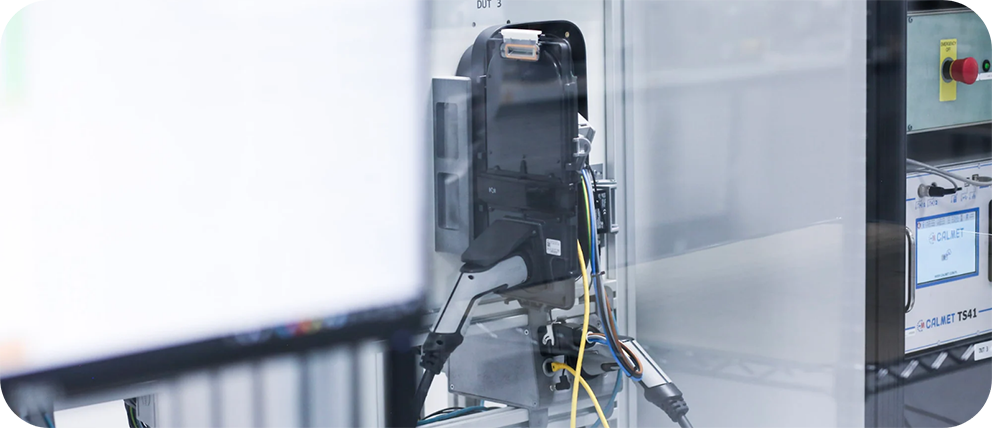
Finally, we load customer firmware onto the system. The installed firmware must be correctly configured and up-to-date so it's ready for use. Once this step is completed, we at Peblar no longer have access to any internal processes of the system for cyber security reasons
Book a consultation with our team
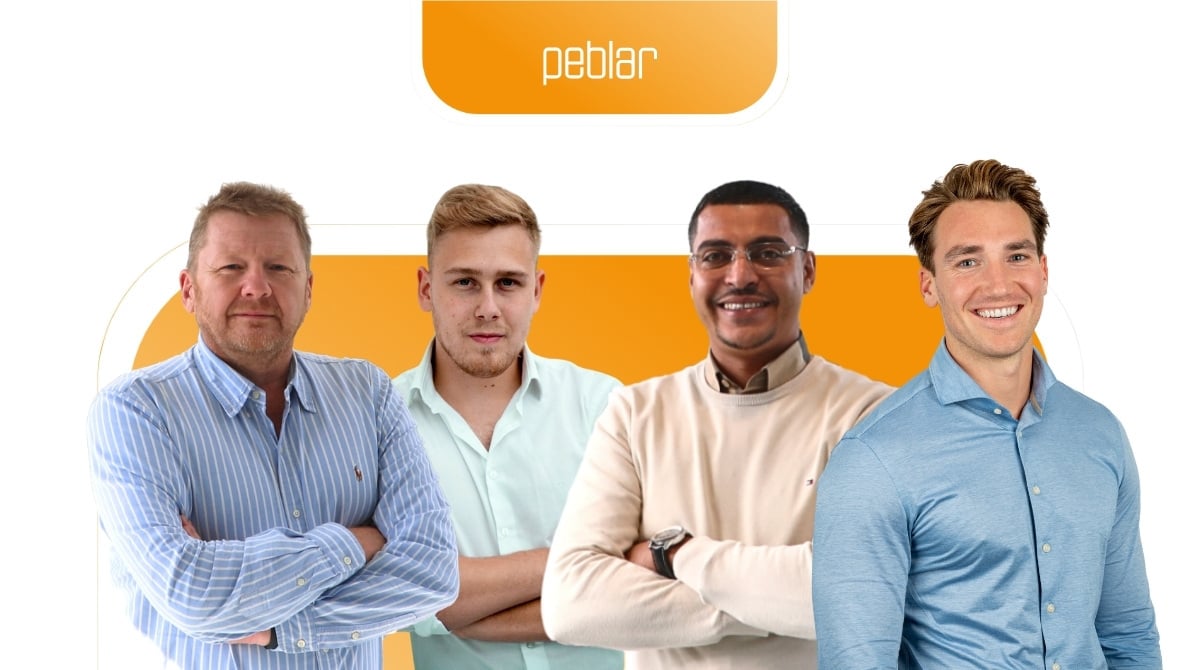
Ready to explore white label options? Schedule a consultation with our team to explore how we can bring your vision to life!
Software configurations
Our goal is to ensure that every charger leaving our facility is future-proof and compatible with software updates. Our chargers must remain robust and reliable for years to come
Regression testing
To verify software builds, we continuously run regression testing throughout the day and night. The goal is to ensure updates run efficiently and the charger continues to operate after various modifications and bug fixes
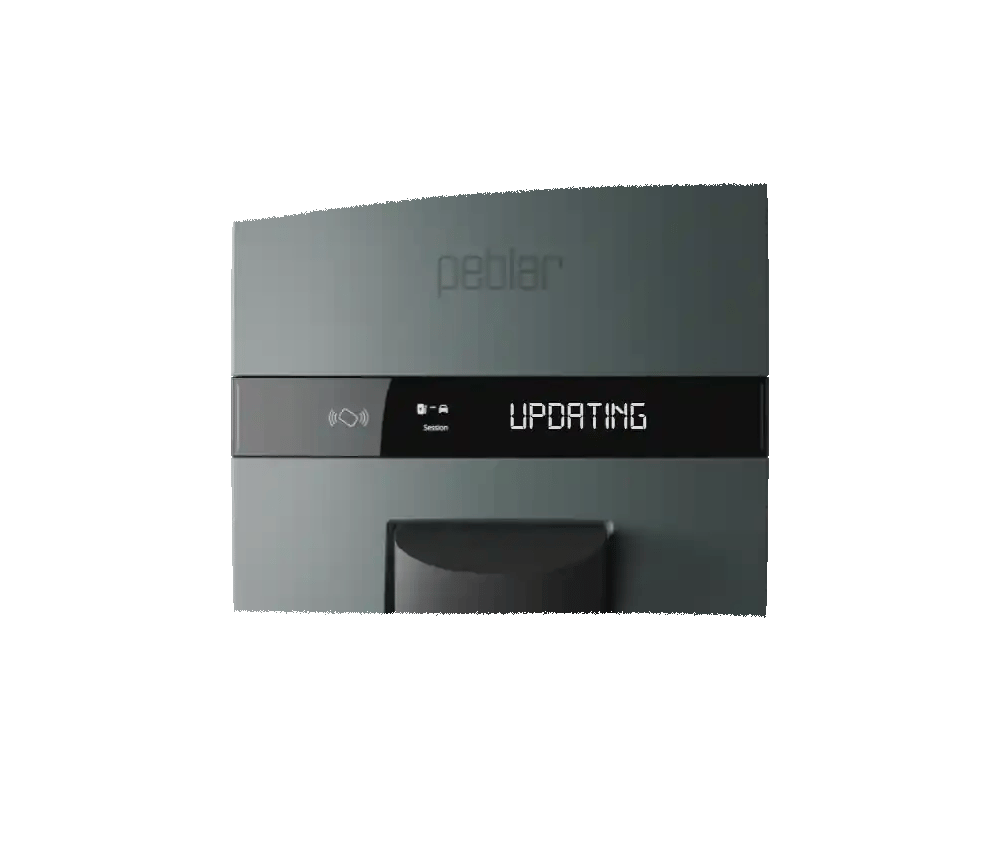
New features and software
Inside our facility, we test new features on a group of chargers using simulated vehicles. Once they pass these initial tests, we take it into the real world: our parking lot at Prodrive. Here, we test the chargers with an array of configurations, from socket to cable versions. We also assess load balancing to ensure all the chargers work together during peak demand
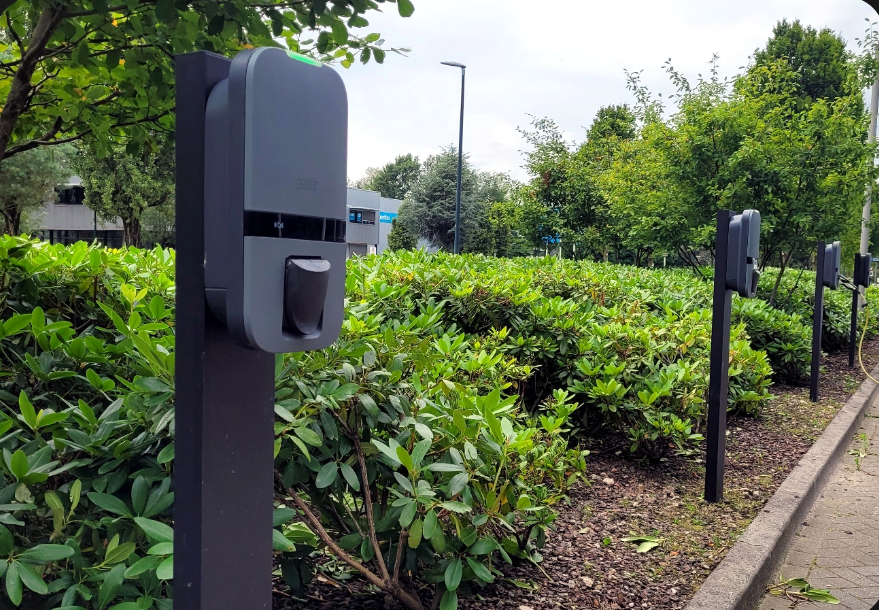
Compatibility with third-party software
At Peblar, we work with a range of external metering devices, including HomeWizard, FLEXECHARGE and Xemex. In our final software test, we ensure our EV chargers work with these energy management platforms so customers can connect their chargers with ease and confidence.
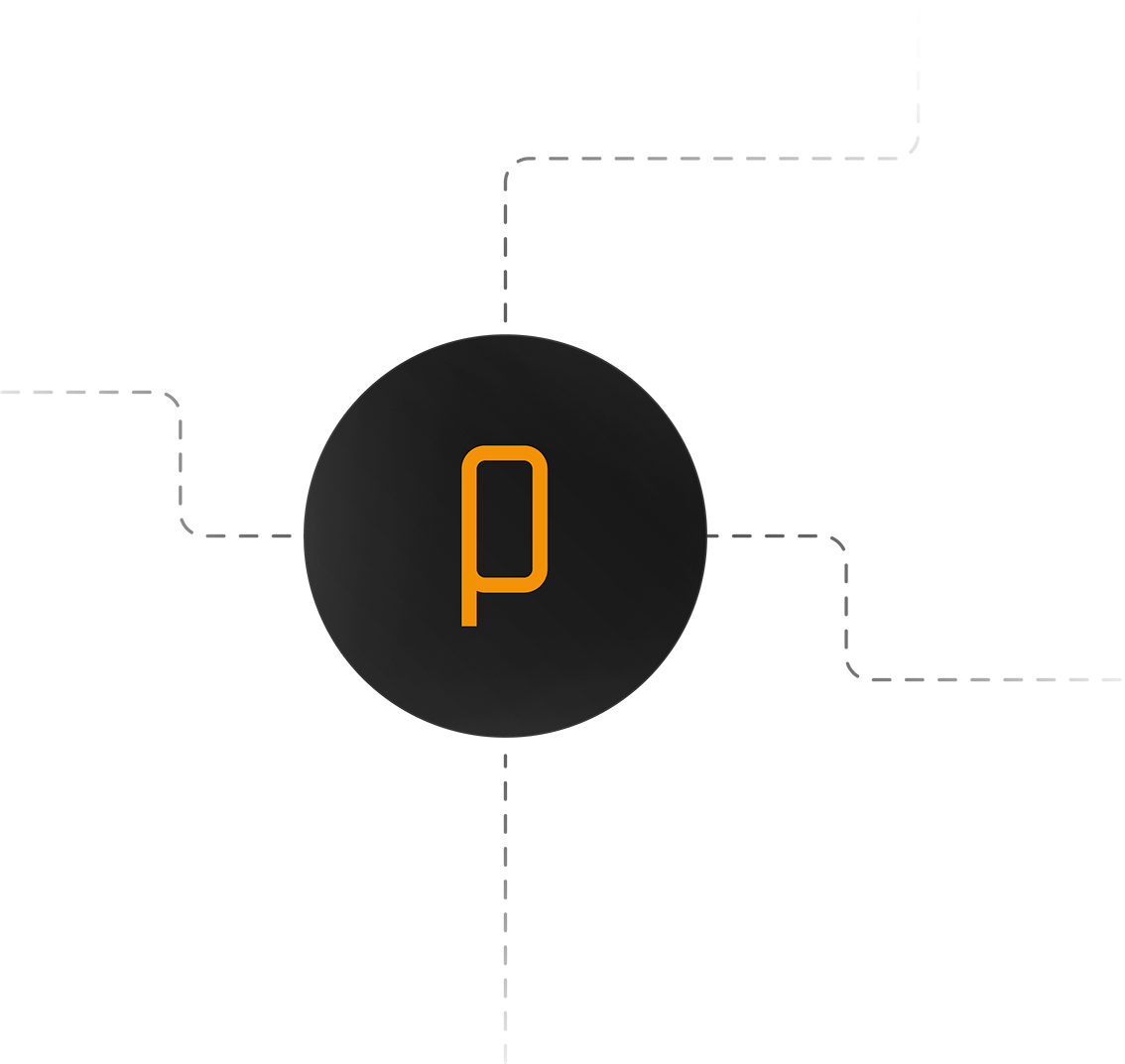
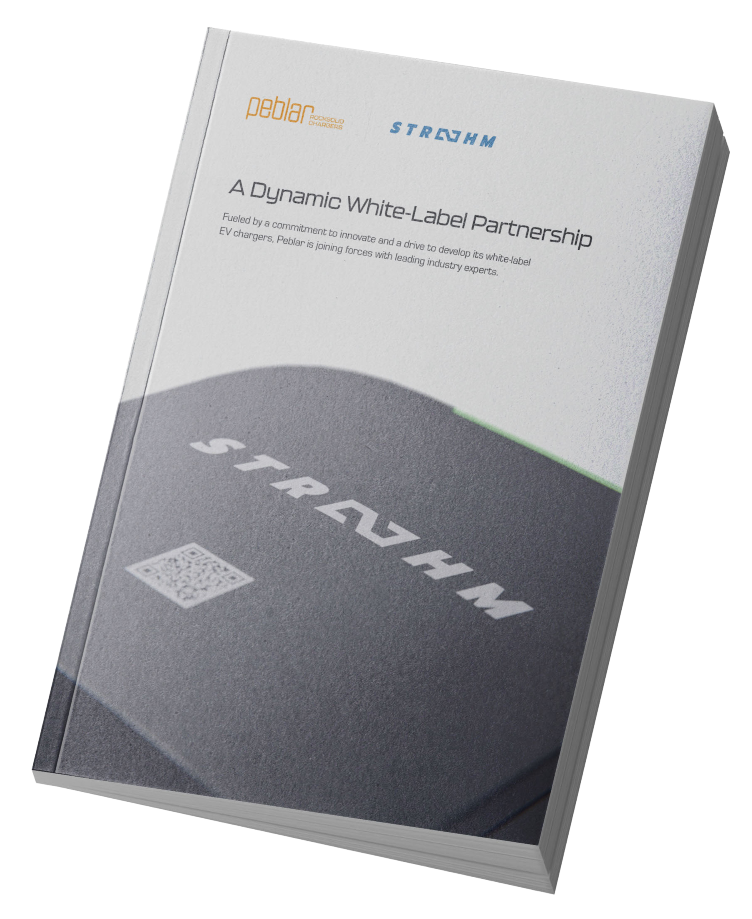
Peblar and STROOHM:
a dynamic white label partnership
Up next:
Test and validation
This stage is carried out before the production process. These environmental tests simulate harsh external conditions including extreme temperatures, vibration and water exposure to test the charger’s durability under stress. This ensures each charger can operate within the toughest conditions, giving our customers reliable performance no matter where they are
Lifetime tests
Accelerated lifetime testing (ALT) simulates 10 years of charger use in just a few months. This includes temperature endurance tests where we heat the chamber to a high temperature and alternate between charging at full operation and standby.
We then cycle between high and freezing temperatures, repeating this process for a couple of months to ensure the charger can stabilise across a range of temperatures
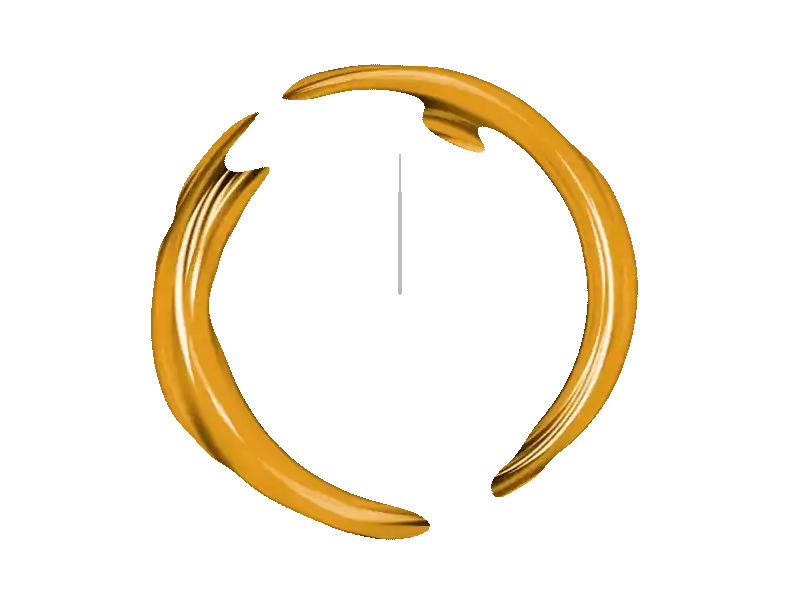
Highly accelerated lifetime testing (HALT)
Hot and cold stress tests push our chargers to their limits by exposing them to extreme hot and cold temperatures until the device breaks. At each temperature setpoint, we wait for a stable temperature and then perform a charging session to test the functionality
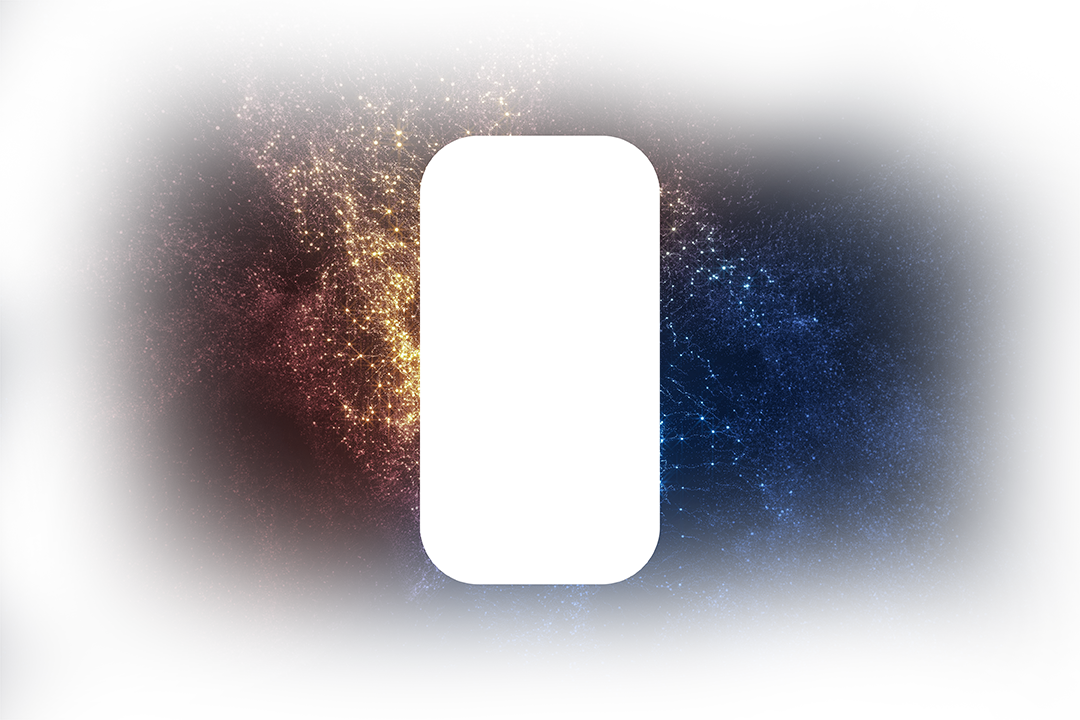
Climatic and environmental tests
We conduct a series of high and low-temperature cycles, alternating between standby and full operation of the charger. Humidity tests are also performed to check for condensation inside the charger.
Testing humidity levels if very important since water ingress can have safety implications. These tests expose the charger to a high relative humidity across the whole temperature range
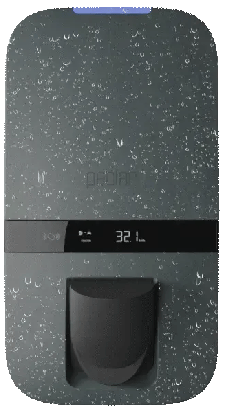
Ingress protection (IP) tests
In our testing chambers, we simulate real-life environmental conditions by exposing the chargers to dust and water, testing for ingress within the device.
Standard IP54 spray testing ensures our chargers can function properly when exposed to rain or dusty conditions without any impact on performance
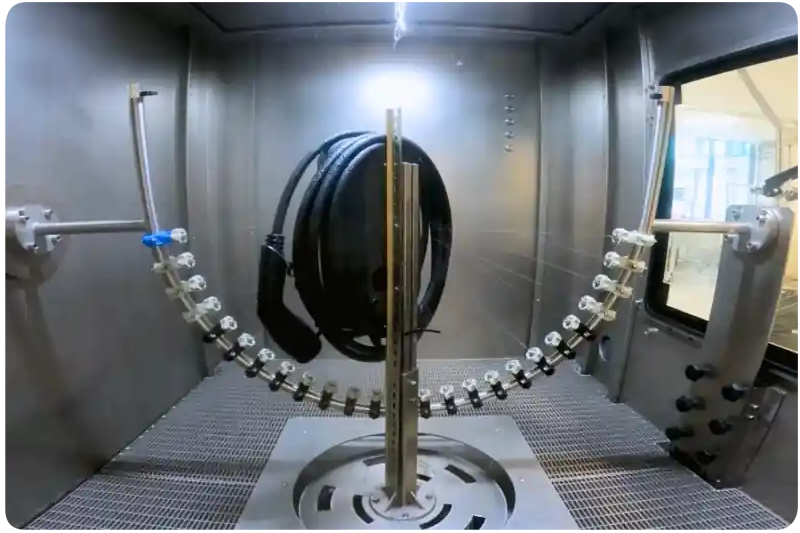
Thermal shock
The charger undergoes rigorous testing through various steep temperature cycles. Once the charger stabilises at each stage, we alternate the heat cycle, repeating this process for hundreds of cycles.
This identifies any weak points in the connections and ensures the charger maintains functionality when exposed to thermal stress
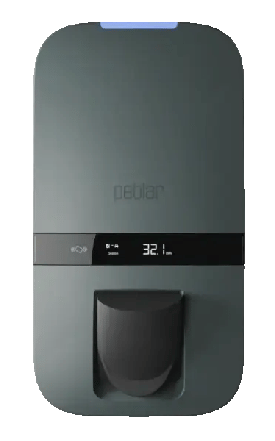
Electromagnetic compatibility (EMC)
This crucial stage ensures our chargers are robust against electromagnetic interference. We test that the EV chargers don’t emit too strong electromagnetic fields that could interfere with other devices.
The charger is placed in a magnetically sealed EMC chamber, where a receiving antenna detects emissions from various angles
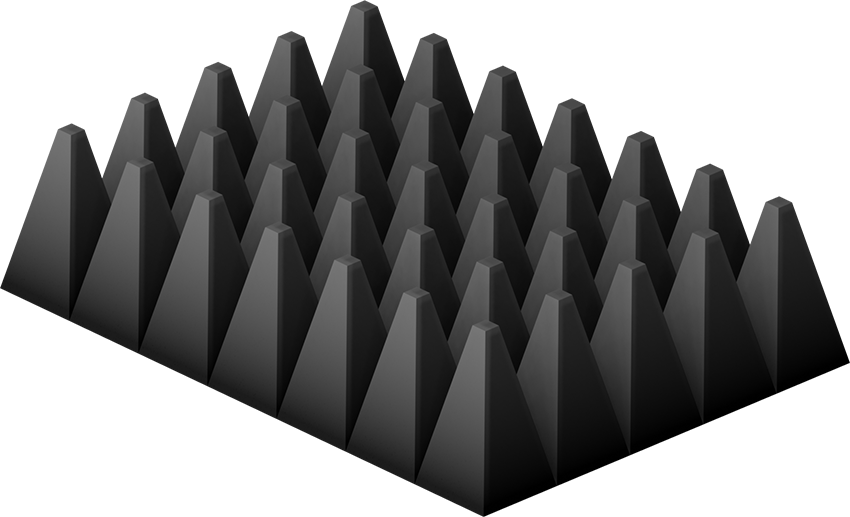
Mechanical testing: IK and vibration
These tests assess the durability of the charger’s components against physical shock and impact. Drop tests include a free fall of the device onto a concrete floor to ensure the housing remains intact and undamaged.
Mechanical impact resistance is tested up to an IK10 rating, applying severe impacts on the surface of the EV charger and we test the functionality before and after the impact
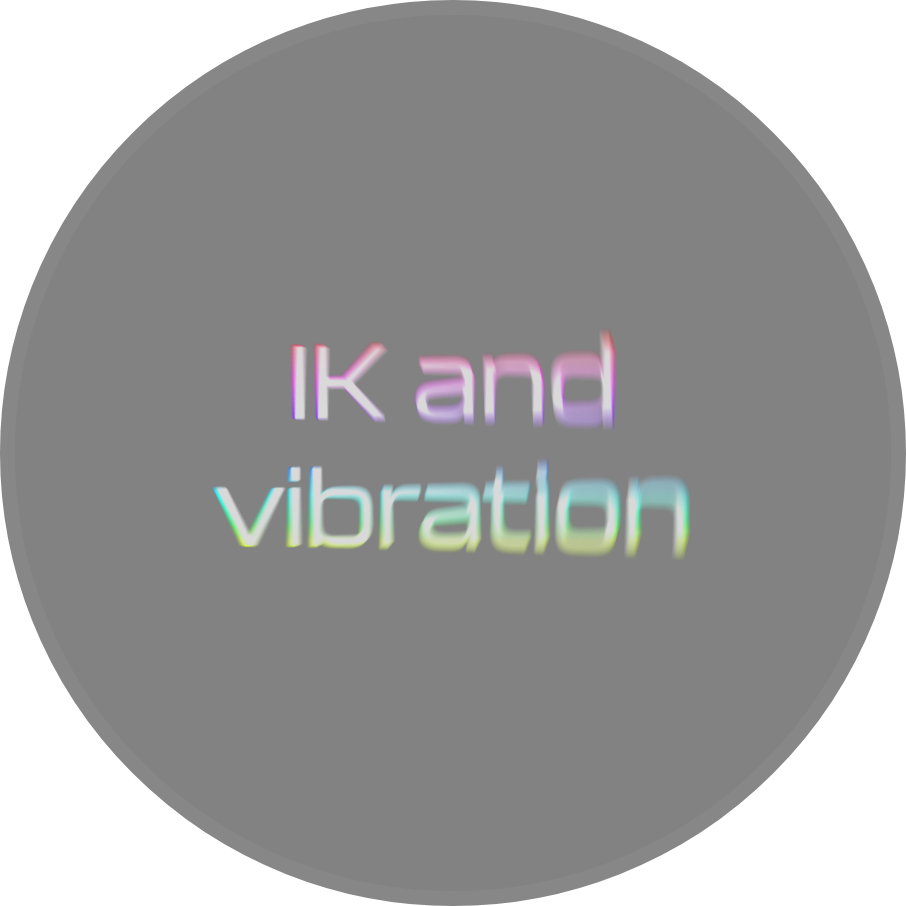
.jpg?width=1200&height=670&name=Team%20France%20(1).jpg)
Book a consultation with our team
Ready to explore white label options? Schedule a consultation with our team to explore how we can bring your vision to life!