The core of Peblar chargers: Inside the printed circuit board assembly (PCBA)
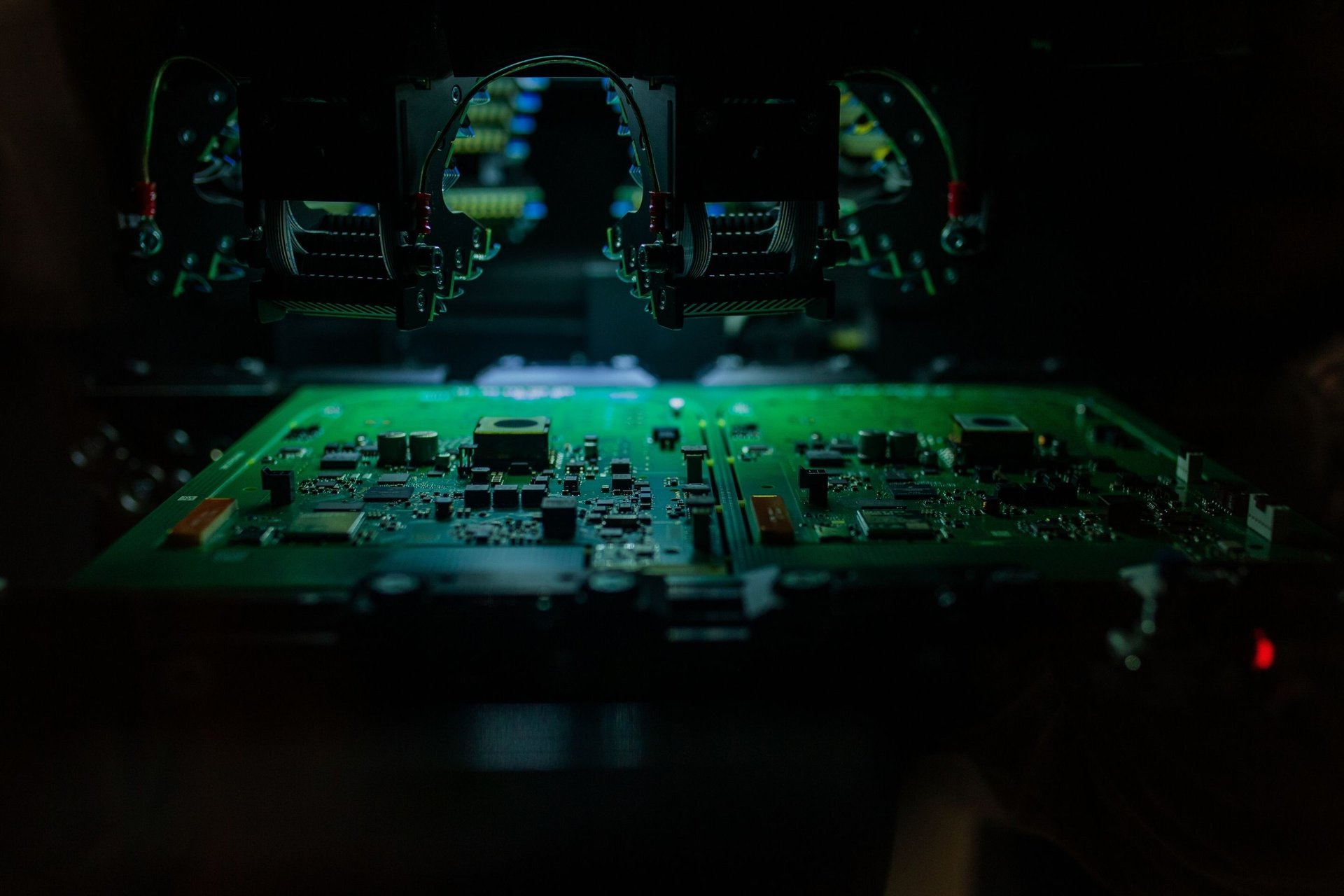
At Peblar, we believe that excellence starts at the very heart of our chargers: the printed circuit board (PCB). Unlike many in the industry, we take pride in manufacturing the printed circuit board assembly (PCBA) ourselves. This approach gives our engineers full control over production, ensuring that each and every Peblar charger meets our exact standards.
The heart of every charger
The PCBA isn’t just another part - it’s the core of every charger. Each one is made up of over 1.200 components, all carefully assembled to make sure each EV charger performs flawlessly. By keeping the PCBA manufacturing process in-house, we can make real-time improvements and ensure precision at every stage.
Each circuit board undergoes rigorous testing at various stages, including four visual inspections (solder paste, placement, soldering, through-hole), X-rays and automatic electrical tests (AET). We’re not just meeting industry standards, we’re exceeding them - delivering chargers that are built to last.
Technology that ensures quality
We begin the manufacturing in the surface mounted device (SMD) department, where the tiniest components are precisely soldered onto the circuit board. Imagine it like a carefully coordinated dance of machines and engineers which achieves unmatched accuracy. Each step is backed by inspections to reveal even the hidden flaws that may be hidden to the human eye.
Once the small components are in place, our engineers move to the through-hole soldering process. Our attention to detail ensures that no defect goes unnoticed, saving time, cost and materials by catching issues early. This dedication to detail means that when you plug in a Peblar charger, you can trust that its core has been rigorously tested and validated.
"We believe the earlier you find a defect, the cheaper and easier it is to fix. We start optical inspections as early as when the solder paste is printed, taking pictures at every step.”
Bram Schroeders, mechanical engineer
Beyond the board: Building for durability
Our commitment doesn’t stop at assembling and testing the PCBA. Every Peblar charger is designed to last and the extensive environmental tests run during the development stage ensures performance in tough external climates.
From building injection-moulded casings that protect against water and dust to climate tests that simulate years of wear and tear, every charger is tested to the extreme. It’s all about making sure our EV chargers are not just robust but also seamlessly integrated into your world.
End-to-end excellence
From the PCBA to the final setup, every step in the process is supported through quality checks. Our vertically integrated facility at Prodrive Technologies allows us to adapt quickly and refine processes so every charger meets high standards of reliability.
When you plug in a Peblar charger, you’re not just using a device, you’re experiencing the result of innovation and a commitment to excellence. It’s the Peblar promise: built into every circuit, tested at every stage and designed to power your journey. Take a closer look inside our testing facility and discover how our chargers come to life.